Efficiency in separation. Lamellar pack oil separators are very effective in separating oils and light hydrocarbons precisely because of the inclined lamellae within the system.
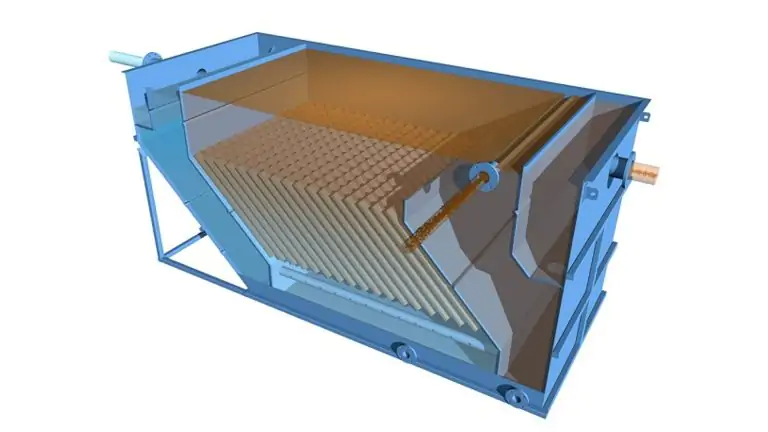
Oilpack Lamella-Pack Oil Separators
for process oil removal
Lamella-pack oil separators, often installed already at the primary treatment level, prevent particularly environmentally harmful components such as oils and hydrocarbons from reaching water bodies at the time of spillage. Slats inclined at 45° make the system efficient. Separated substances can also be recovered for better cost-effectiveness of the whole system.
Low investment costs. Simple design, installation, operation. Costs can be further cut by providing an appropriately sized storage tank upstream, minimizing the size of the oil separator.
Oil recovery. Following separation, Oil Separators can recover the separated oils and light hydrocarbons to enable easy recycling or disposal.
Energy savings. Lamella-pack oil separators have a lower cost, in terms of energy resources, than some other oil separation solutions.
Compact design. Lamellar pack oil separators do not require large tanks or reservoirs, making them suitable for installations in confined spaces: for example, parking lots, machine shops and industrial areas.
Adaptability. These are systems suitable for civil and industrial wastewater treatment in extremely heterogeneous sectors.
Lamella-pack oil separators: description and operation
Lamella-pack oil separators perform a fundamental function in wastewater treatment, namely the separation of components that are particularly harmful (oils and hydrocarbons) to water bodies. They are devices used in both civil and industrial settings: in municipal wastewater treatment plants they often intervene at the primary treatment level, upstream from further water purification and finishing technologies.
How do lamella-pack oil separators work?
- The flow of water and oil is fed into the tank and evenly distributed over the entire section.
- Below the inlet area are placed the lamellar packs, inclined at 45°. The single oil particle, which has lower density than water, tends to rise to the surface. Instead, the clarified water flows through the lamella pack, with fine reeds, with gravitational motion (from top to bottom) with uniform velocity and flow rate within each channel.
- Upon reaching the surface, oil particles accumulate in the central area of the tank, above the lamellar pack; from here they are extracted with an oil-skimmer.
- The clarified and de-oiled water, taken up from below the lamella pack, reaches the free surface on the side opposite the feed side and from there is conveyed to the outside, to the discharge or to any subsequent treatment.
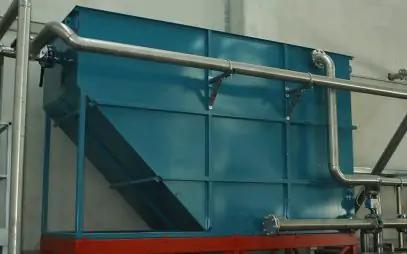
Lamella-Pack Oil Settlers: Applications
Learn about installation contexts hereDo you need info?
We wish to support you with our technologies: we are always happy to forward technical and commercial information and explanatory materials.
Ask for informationDownloads
Our range of oil separators
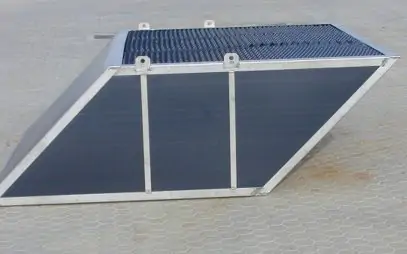
Oilpack Oil Separators with O-Frame
MITA Water Technologies offers an oil separation option with only lamella pack enclosed in a stainless steel frame. This system can be installed in existing tanks or in new specially made tanks, resulting in a complete oil separation system.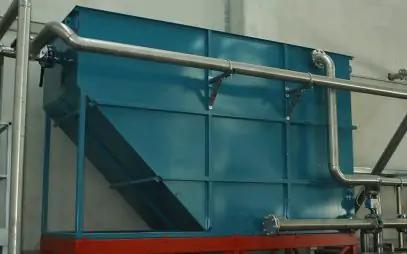
Oilpack Oil Separators Monoblock OM
These one-piece oil separators are designed to separate non-emulsified oils and consist of a containment tank, made of treated and painted carbon steel or AISI 304 stainless steel or stainless steel according to the customer's choice, and a 45° inclined parallel channel lamella pack made of UV-resistant polystyrene. Customizations with special materials are available upon request.Alcune realizzazioni MITA
- Industrial Wastewater
- Suspended Solid Removal
- BOD and COD Removal
- Oil and Grease Removal
- Biorulli® Biodiscs
- Dissolved Air Flotation Units
- Continuous Sand Filters
Water Treatment and Cooling Systems for Vedani Group
Various industrial water treatment technologies as well as cooling technologies: since 1995 MITA Water Technologies has provided multiple solutions, together with its "sister" company MITA Cooling Technologies, for the complete water management of Vedani Group, which has been active in aluminum processing since 1982.
Read moreBiological Rotors for the Chemical Company Icap-Sira
High efficiency, ease of installation, and extreme operation-these are the features that a well-known company in the chemical industry appreciated in choosing Biorulli® biodiscs for the biological oxidation of its wastewater. MITA Water Technologies has been cooperating with this industry since 2006.
Read moreBiorulli® Rotating Biological Contactors for ENI
Customization and long-term trust relationship: these are the two variables that decided the award to MITA Water Technologies of the revamping of the water treatment of an ENI depot in Central Italy. Rotary biological contactors, supplied to the company, are simple but efficient devices for COD removal.
Read moreWould you like a noncommittal consultation?
Tell us about your project in wastewater treatment or tertiary filtration.
Contact us nowWhat is your process goal?
Tools to help you choose
Industrial and civil wastewater treatment technologies
Our support throughout the product life cycle
A sustainable and efficient solution for every industry and need
Resources
Needs of wastewater treatment
Discover the solution for all needsComparing different technologies
Find out all the different technologiesFind out more
All technical articlesOr You Can Choose
Our Newsletter
Sign up for the MITA Water Technologies newsletter: stay up-to-date on systems for municipal and industrial wastewater treatment and filtration.